Definition and Basics of Magnetic Chamfers
A magnetic chamfer is a specialized magnetic formwork component designed to create beveled edges or corners in precast concrete structures. These innovative tools utilize powerful rare earth magnets (typically neodymium) embedded within a durable steel or polymer housing that attaches securely to steel formwork surfaces during the concrete casting process.
Unlike traditional wooden or plastic chamfer strips that require mechanical fastening, magnetic chamfers adhere instantly to steel forms through magnetic force, creating precise 45° or custom-angled beveled edges on concrete elements. These bevels serve both aesthetic and functional purposes, eliminating sharp corners that could chip or cause injury while enhancing the visual appeal of finished concrete products.
Key Components of a Magnetic Chamfer:
-
High-strength neodymium magnets that provide secure attachment
-
Durable housing (typically steel or high-impact polymer)
-
Precision-engineered angles (commonly 45°, but also available in other specifications)
-
Non-stick surfaces for clean concrete release
-
Various size options to accommodate different project requirements
Magnetic chamfers represent a significant advancement in concrete forming technology, offering precision, reusability, and efficiency that traditional methods cannot match. For precast concrete manufacturers, these tools have become an essential component in modern production processes.
How Magnetic Chamfers Work in Precast Concrete
Magnetic chamfers operate on a simple yet effective principle based on powerful magnetic attraction. When placed against steel formwork, the embedded magnets create a strong bond that keeps the chamfer firmly in position during the entire concrete pouring and curing process. This magnetic action eliminates the need for adhesives, screws, nails, or other fastening methods that can be time-consuming and may damage forms.
The Working Process:
-
Preparation: Clean the steel formwork surface to ensure no debris interferes with magnetic contact.
-
Positioning: Place the magnetic chamfer along edges where bevels are desired, allowing the magnetic force to secure it in place.
-
Concrete Casting: Pour and vibrate concrete as normal, with the chamfer remaining firmly in position.
-
Formwork Removal: After concrete sets, the formwork and magnetic chamfers are easily separated from the concrete.
-
Result: A clean, precise chamfered edge is left on the concrete element.
The magnetic strength is carefully calibrated to provide secure attachment during use while still allowing for easy removal when needed. Most quality magnetic chamfers are engineered to withstand the pressure and vibration of concrete pouring without shifting, ensuring consistent results across large production runs.
This magnetic attachment method provides significant advantages over traditional systems, particularly in precast concrete operations where efficiency and repeatability are paramount. The absence of adhesives also means there's no residue to clean up afterward, reducing maintenance time and costs.
Types of Magnetic Chamfers Available
The precast concrete industry utilizes several types of magnetic chamfers, each designed for specific applications and requirements. Understanding the differences between these types can help manufacturers select the optimal solution for their projects.
Based on Profile Shape:
-
Standard 45° Chamfers: The most common type, creating a 45-degree bevel on concrete edges.
-
Custom Angle Chamfers: Available in angles ranging from 15° to 60° for specialized architectural requirements.
-
Radius Chamfers: Create rounded rather than angled edges for a softer appearance and improved safety.
-
Decorative Profile Chamfers: Feature various ornamental profiles for architectural concrete elements.
Based on Material Construction:
-
Steel-Bodied Chamfers: Extremely durable with high magnetic strength, suitable for heavy-duty applications.
-
Polymer-Encased Chamfers: Lightweight with non-stick properties, ideal for intricate designs and easier handling.
-
Hybrid Chamfers: Combine metal and polymer components to balance strength and weight.
Based on Size and Length:
-
Standard Production Lengths: Typically available in 1-3 meter lengths for efficient production.
-
Custom-Length Chamfers: Can be manufactured to specific dimensions for unique project requirements.
-
Corner Connection Systems: Specialized magnetic chamfers designed for corner junctions, ensuring clean intersections.
Chamfer Type |
Best For |
Typical Magnetic Strength |
Reusability |
Steel Standard 45° |
High-volume precast production |
Very High |
1000+ cycles |
Polymer Custom Angle |
Architectural elements |
Medium |
500+ cycles |
Hybrid Radius |
Safety-critical applications |
High |
800+ cycles |
Decorative Profile |
Ornamental concrete elements |
Medium-High |
400+ cycles |
At Horizon Magnetic, we offer a comprehensive range of magnetic chamfers to meet diverse precast concrete manufacturing needs, from standard production models to highly specialized custom solutions.
Benefits of Using Magnetic Chamfers
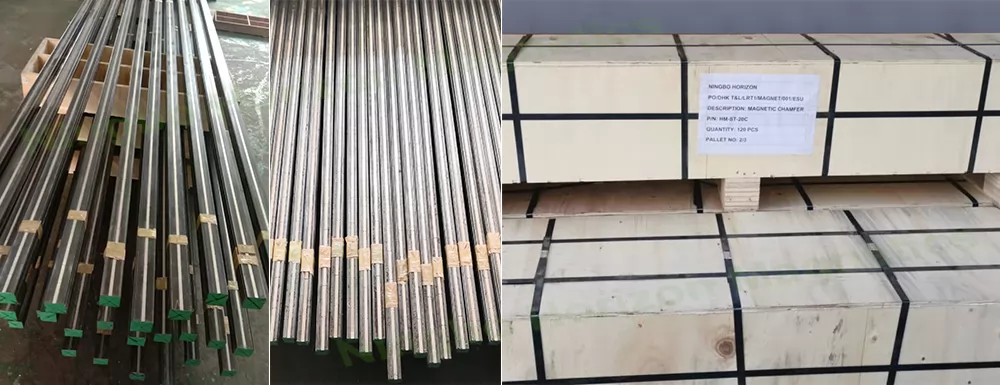
Implementing magnetic chamfers in precast concrete production offers numerous advantages over traditional chamfering methods. These benefits translate to improved operational efficiency, cost savings, and enhanced product quality.
Operational Efficiency
-
Rapid Installation: Magnetic chamfers attach instantly to steel formwork, reducing setup time by up to 80% compared to mechanical fastening methods.
-
Quick Repositioning: Easily adjust placement without damage to forms or time-consuming refastening.
-
Simplified Workflow: Eliminate the need for drilling, nailing, or gluing, streamlining the production process.
-
Reduced Labor Requirements: Faster setup and teardown means fewer man-hours per production cycle.
Cost Benefits
-
Durability: High-quality magnetic chamfers can withstand hundreds or thousands of production cycles, reducing replacement costs.
-
Formwork Preservation: No drilling or nailing means extended formwork life and reduced maintenance expenses.
-
Waste Reduction: Unlike disposable chamfer strips, magnetic versions are reusable, minimizing material waste.
-
Energy Efficiency: Faster production cycles can reduce overall energy consumption in manufacturing facilities.
Quality Improvements
-
Consistent Results: Precise positioning ensures uniform chamfers across all concrete elements.
-
Clean Release: Non-stick surfaces produce sharp, clean edges without concrete adhesion issues.
-
Reduced Defects: Secure attachment prevents shifting during concrete pouring and vibration.
-
Enhanced Aesthetics: Precision-engineered angles create visually appealing, professional finishes.
ROI Analysis: Most precast concrete manufacturers report that magnetic chamfers pay for themselves within 15-30 production cycles through labor savings and reduced material waste. With a typical lifespan of 500+ cycles, the long-term return on investment is substantial.
By incorporating magnetic chamfers into precast concrete production processes, manufacturers can achieve significant improvements in both operational efficiency and product quality while reducing long-term costs.
Installation and Usage Guidelines
Proper installation and use of magnetic chamfers are essential for achieving optimal results in precast concrete applications. Following these guidelines ensures consistent quality, maximizes the lifespan of your magnetic chamfers, and prevents common issues during the production process.
Pre-Installation Preparation
-
Surface Cleaning: Ensure steel formwork surfaces are clean and free from concrete residue, dust, oil, or other contaminants that could interfere with magnetic adhesion.
-
Formwork Inspection: Check that the steel formwork is free from warping or damage that might prevent flush contact with the magnetic chamfer.
-
Chamfer Cleaning: Verify that the magnetic chamfer itself is clean and free from concrete buildup from previous uses.
-
Layout Planning: Measure and mark positions for chamfer placement to ensure proper alignment.
Installation Process
-
Positioning: Hold the magnetic chamfer slightly away from the steel form, then allow it to attract to the surface naturally to prevent impact damage.
-
Alignment: Position the chamfer precisely along the edge where the bevel is required.
-
Connection: When joining multiple chamfer sections, ensure tight, flush connections to prevent concrete seepage between units.
-
Corner Treatment: At corners, use special corner connectors or miter the chamfers at 45° angles for clean intersections.
-
Security Check: Once positioned, test the security of the attachment by applying gentle pressure.
During Concrete Pouring
-
Pour concrete carefully around chamfer areas to avoid displacement.
-
When using concrete vibrators, maintain reasonable distance from chamfers to prevent dislodging.
-
Periodically check chamfer positions during pouring if accessible.
Removal and Cleanup
-
Timing: Remove magnetic chamfers only after concrete has adequately set but before complete curing for optimal release.
-
Technique: Use a gentle prying motion starting at one end rather than pulling the entire length at once.
-
Cleaning: Immediately clean any concrete residue from the chamfer using appropriate tools without damaging the magnetic components.
-
Storage: Store cleaned chamfers in a dry, organized area away from heavy machinery that could damage them.
Safety Note: Always handle magnetic chamfers with care, particularly around sensitive electronic equipment. The strong magnetic fields can potentially affect pacemakers and other medical devices. Use appropriate personal protective equipment when cleaning chamfers to avoid injury from sharp concrete fragments.
By following these installation and usage guidelines, precast concrete manufacturers can maximize the effectiveness and lifespan of their magnetic chamfer systems while ensuring consistent, high-quality beveled edges on concrete products.
Common Applications in Precast Concrete Industry
Magnetic chamfers have revolutionized numerous applications within the precast concrete industry, providing efficient and precise edge detailing across a wide range of products. Their versatility makes them valuable tools in various precast concrete manufacturing scenarios.
Structural Precast Elements
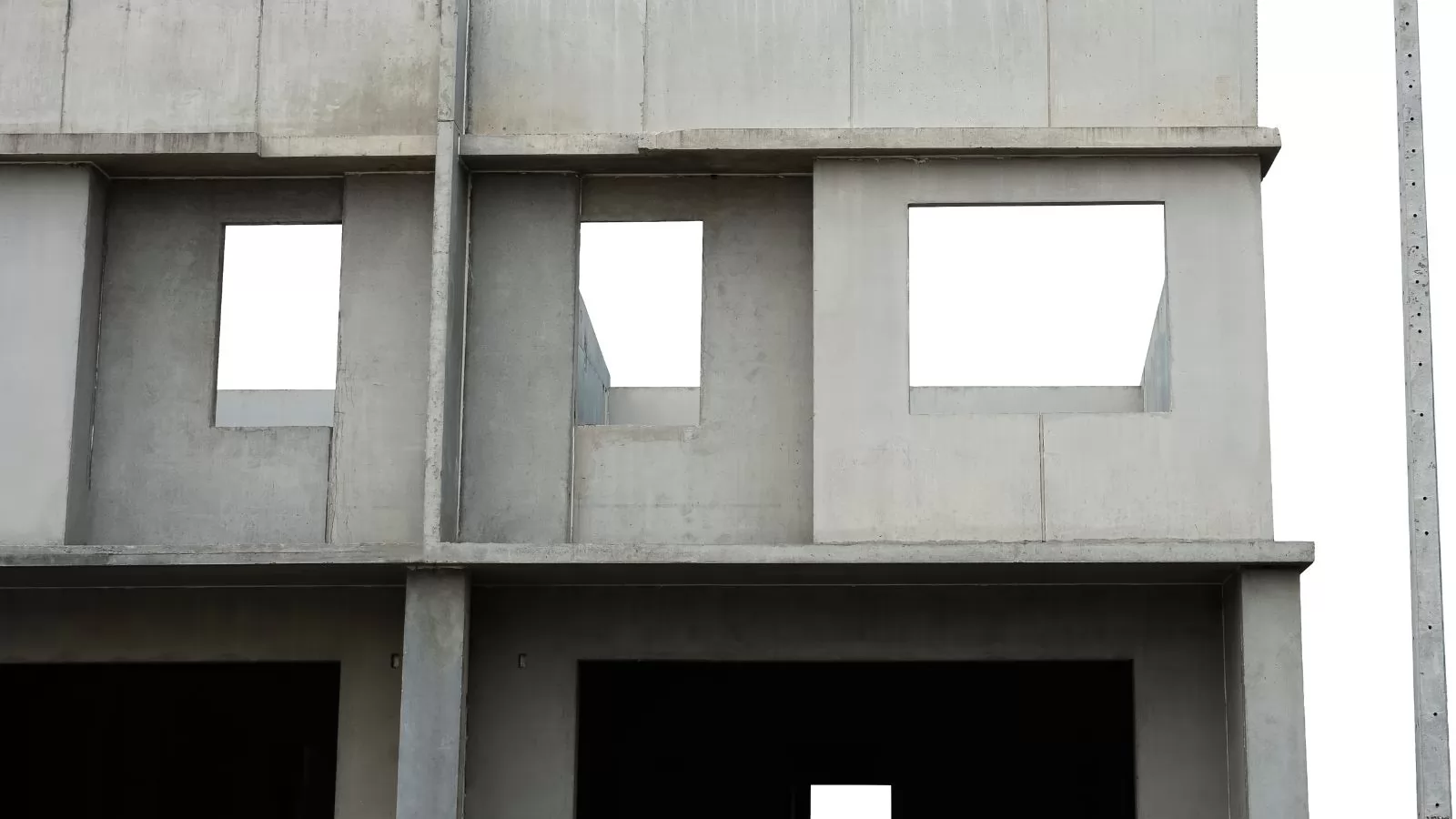
-
Concrete Panels: Creating clean, chamfered edges on wall panels, façade elements, and cladding components.
-
Columns and Beams: Providing safety bevels on structural elements while enhancing aesthetic appeal.
-
Foundation Components: Adding chamfered edges to footings, grade beams, and pile caps for improved handling and appearance.
-
Flooring Systems: Creating beveled edges on floor slabs, stairs, and landings to reduce chipping risk.
Transportation Infrastructure
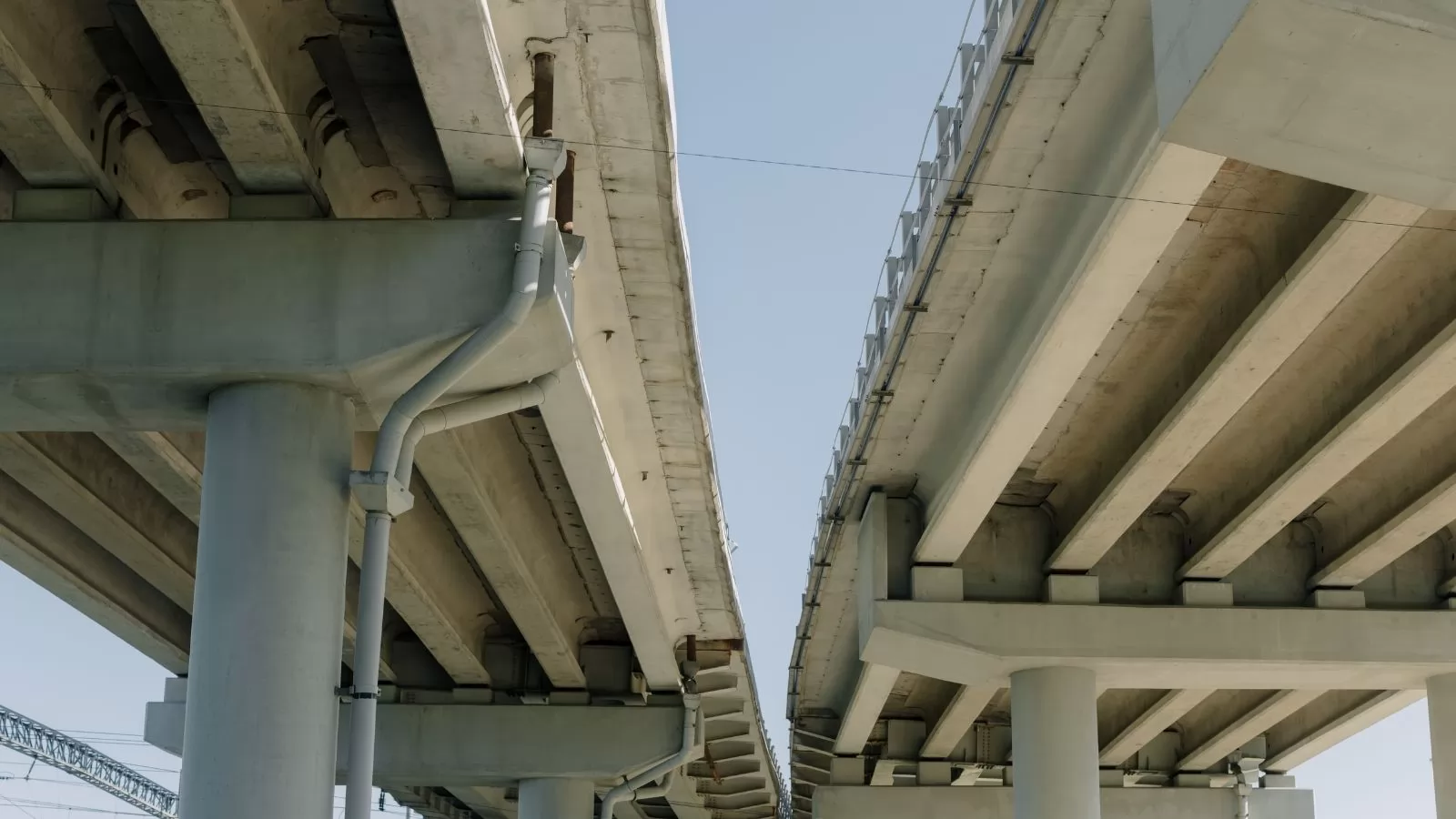
-
Bridge Components: Manufacturing beveled edges on girders, deck panels, and abutment elements.
-
Traffic Barriers: Creating chamfered edges on Jersey barriers, sound walls, and traffic dividers.
-
Railway Elements: Producing sleepers/ties and platform components with consistent chamfered edges.
-
Tunnel Segments: Adding precise bevels to curved precast tunnel lining segments.
Architectural Precast
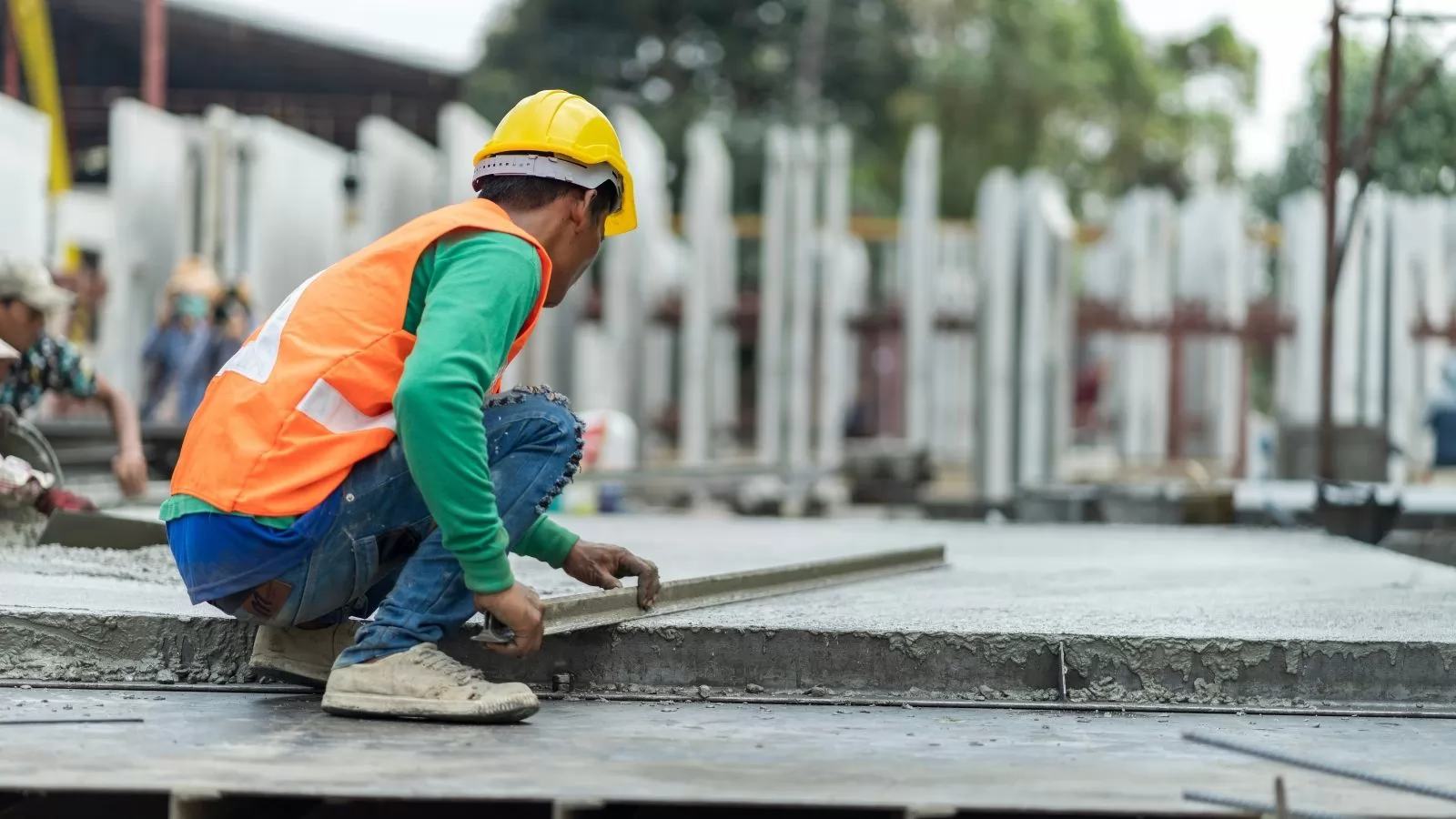
-
Decorative Panels: Creating clean bevels on architectural façade elements and decorative concrete features.
-
Urban Furniture: Manufacturing benches, planters, and other street furniture with safety-conscious chamfered edges.
-
Water Features: Producing fountain components, pools, and water management structures with precision bevels.
-
Custom Architectural Elements: Facilitating unique designs that require consistent edge treatment.
Utility and Infrastructure
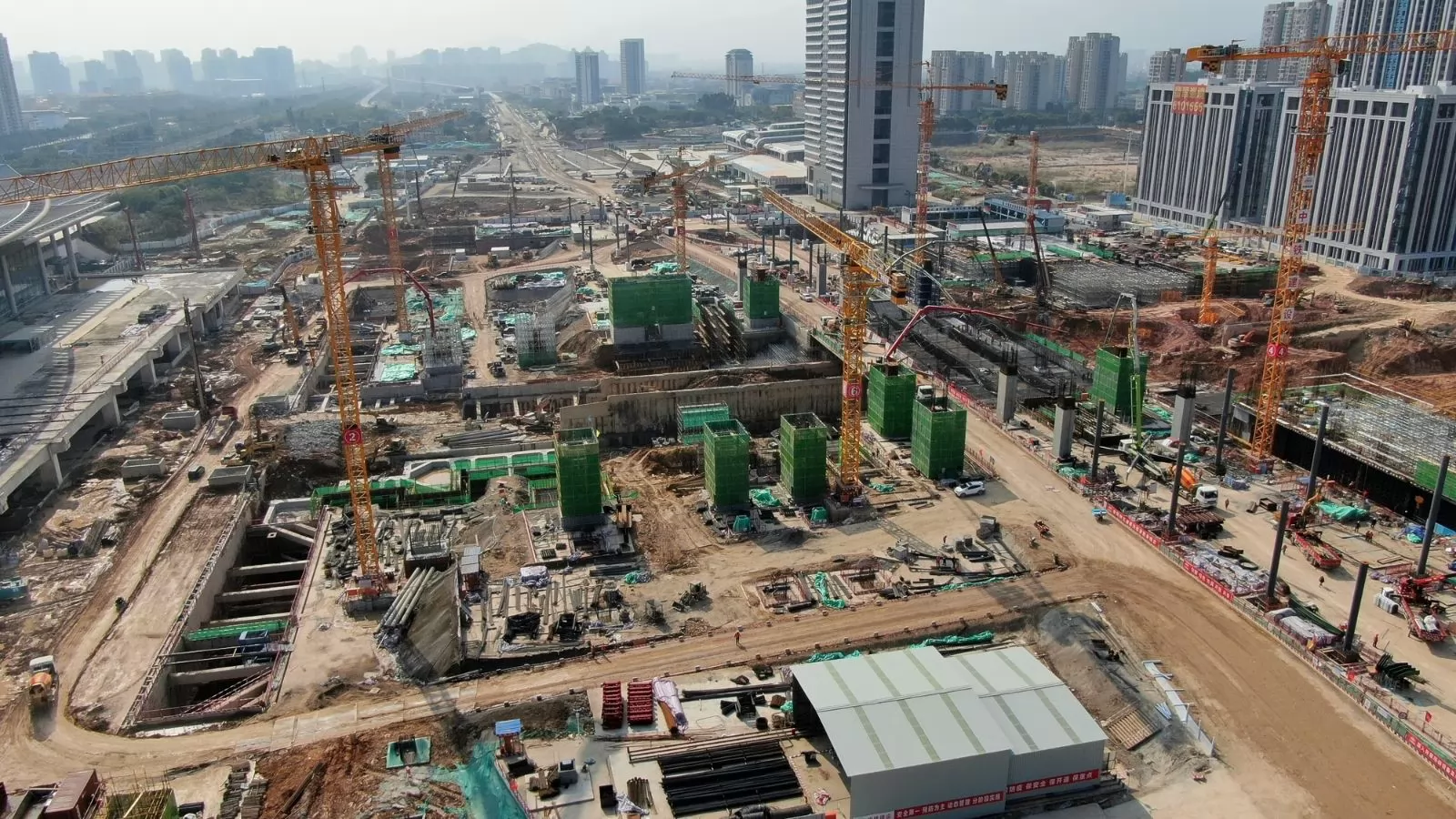
-
Manholes and Access Chambers: Creating beveled edges on utility access components.
-
Drainage Systems: Manufacturing culverts, catch basins, and drainage channels with chamfered edges for improved flow characteristics.
-
Electrical Infrastructure: Producing transformer pads, utility vaults, and equipment housings with safety bevels.
-
Water Treatment: Creating tanks, clarifiers, and treatment plant components with consistent edge detailing.
In each of these applications, magnetic chamfers provide not only aesthetic benefits but also practical advantages such as improved safety (by eliminating sharp edges), enhanced durability (by reducing the risk of edge chipping), and better functionality (by facilitating assembly or improving flow characteristics in hydraulic applications).
The versatility of magnetic chamfers makes them indispensable tools in modern precast concrete production, contributing to higher-quality products across virtually all market segments.
Maintenance and Care Instructions
Proper maintenance of magnetic chamfers is essential for maximizing their service life and ensuring consistent performance in precast concrete applications. Following these maintenance and care guidelines will help preserve your investment and maintain production quality.
Daily Maintenance
-
Post-Use Cleaning: After each use, promptly remove any concrete splatter or residue before it hardens.
-
Cleaning Method: Use plastic scrapers rather than metal tools to avoid scratching the chamfer surface.
-
Rinse Thoroughly: Use clean water to remove fine concrete dust after scraping.
-
Drying: Thoroughly dry chamfers before storage to prevent corrosion of magnetic components.
Weekly Maintenance
-
Deep Cleaning: Apply approved concrete release agents to stubborn residue, allowing it to penetrate before gentle removal.
-
Surface Inspection: Check for any damage to the chamfer profile that might affect concrete finish quality.
-
Magnetic Strength Test: Verify that magnetic attachment remains strong and consistent along the entire length.
-
Connection Check: Inspect any connectors or joining mechanisms for damage or wear.
Monthly Maintenance
-
Release Agent Application: Apply a thin coat of appropriate release agent to enhance concrete separation and protect surfaces.
-
Structural Inspection: Check for any deformation, bending, or warping that could affect performance.
-
Magnetic Component Inspection: Ensure all magnetic elements remain securely embedded in the housing.
-
Storage Audit: Verify that storage conditions remain appropriate, with chamfers protected from impact, moisture, and extreme temperatures.
Troubleshooting Common Issues
Problem |
Possible Cause |
Solution |
Reduced magnetic strength |
Concrete buildup between magnet and steel form |
Thorough cleaning of contact surfaces |
Inconsistent chamfer profile |
Physical damage or warping |
Repair or replace damaged sections |
Concrete sticking to chamfer |
Insufficient or deteriorated release agent |
Apply fresh release agent before each use |
Chamfer displacement during pouring |
Excessive vibration or weakened magnets |
Adjust vibration technique or replace magnetic components |
Long-Term Care
-
Storage Environment: Store in a clean, dry area away from direct sunlight and extreme temperatures.
-
Positioning: Store horizontally on flat surfaces to prevent warping or bending.
-
Separation: Use dividers between stacked chamfers to prevent magnetic interaction and potential damage.
-
Documentation: Keep records of usage cycles and maintenance to anticipate replacement needs.
With proper maintenance and care, quality magnetic chamfers from Horizon Magnetic can deliver hundreds or even thousands of production cycles while maintaining consistent performance and concrete finish quality.
How to Select the Right Magnetic Chamfer
Choosing the optimal magnetic chamfer for your precast concrete application requires careful consideration of several factors. This selection guide will help you identify the most appropriate magnetic chamfer solution for your specific manufacturing needs.
Assessment Criteria
-
Application Requirements:
-
Identify the specific precast elements you'll be manufacturing
-
Determine the required chamfer size and angle (standard 45° or custom)
-
Consider whether the application is structural, architectural, or utilitarian
-
Evaluate any special environmental conditions (e.g., exposure to chemicals, freeze-thaw cycles)
-
Production Volume:
-
Estimate the number of production cycles the chamfer will undergo
-
Higher production volumes justify more durable (and typically more expensive) chamfer options
-
Consider whether production is continuous or intermittent
-
Formwork Compatibility:
-
Verify the type and thickness of steel formwork being used
-
Assess the formwork surface condition (new, used, coated, etc.)
-
Consider formwork curvature if applicable (some chamfers work better on flat surfaces than curved)
-
Concrete Mix Characteristics:
-
Consider the concrete slump and aggregate size
-
Evaluate whether self-compacting concrete or standard vibrated mixes will be used
-
Assess if specialized concrete types (fiber-reinforced, heavyweight, etc.) affect chamfer selection
Magnetic Strength Considerations
The required magnetic strength varies based on several factors:
-
For vertical formwork: Higher magnetic strength needed to overcome gravity
-
For heavy vibration: Stronger magnets required to prevent displacement
-
For thicker formwork: Magnetic strength decreases with distance, so more powerful magnets needed for thicker forms
-
For safety-critical applications: Higher magnetic strength provides added security against failure
Selection Decision Matrix
Factor |
Steel Magnetic Chamfer |
Polymer Magnetic Chamfer |
Hybrid Magnetic Chamfer |
Durability |
Highest (1000+ cycles) |
Good (300-500 cycles) |
Very Good (500-800 cycles) |
Weight |
Heaviest |
Lightest |
Moderate |
Magnetic Strength |
Strongest |
Moderate |
Strong |
Cost |
Highest initial investment |
Lowest initial cost |
Moderate cost |
Best For |
High-volume production, critical applications |
Lighter-duty applications, complex shapes |
Balanced performance needs |
Custom vs. Standard Solutions
Consider whether your application requires:
-
Standard Chamfers: More economical, readily available, suitable for most common applications
-
Custom Chamfers: Tailored to specific angles, sizes, or profile shapes for specialized applications
At Horizon Magnetic, our technical team can assist in evaluating your specific requirements and recommending the optimal magnetic chamfer solution. We consider factors such as production volume, concrete specifications, and formwork conditions to ensure you select the most appropriate product for your manufacturing process.
Comparison with Traditional Chamfer Methods
Understanding how magnetic chamfers compare to traditional chamfering methods can help precast concrete manufacturers make informed decisions about upgrading their production processes. This comparison highlights the key differences in performance, efficiency, and cost-effectiveness.
Traditional Chamfer Methods
Conventional approaches to creating chamfered edges in precast concrete typically include:
-
Wooden Strips: Cut to size and mechanically fastened to formwork
-
Plastic/PVC Chamfer Strips: Attached with adhesives or mechanical fasteners
-
Metal Angle Strips: Welded or bolted to steel formwork
-
Rubber Chamfer Profiles: Temporarily adhered to formwork surfaces
Comparative Analysis
Aspect |
Magnetic Chamfers |
Traditional Methods |
Installation Time |
Fast (seconds per linear meter) |
Slow (minutes per linear meter) |
Attachment Method |
Magnetic force - no tools required |
Mechanical fasteners, adhesives, welding |
Repositioning Capability |
Instant and damage-free |
Time-consuming, may damage formwork |
Precision |
Highly precise and consistent |
Variable, dependent on installation accuracy |
Reusability |
Hundreds to thousands of cycles |
Limited reuse (10-50 cycles typical) |
Formwork Damage |
None - non-invasive attachment |
Potential damage from fasteners/adhesives |
Initial Cost |
Higher initial investment |
Lower initial cost |
Long-term Cost |
Lower (due to reusability and efficiency) |
Higher (replacement and labor costs) |
The adoption of magnetic chamfers represents a significant advancement in precast concrete production technology, offering substantial advantages in terms of efficiency, precision, and long-term cost-effectiveness despite the higher initial investment.
Conclusion and Recommendations
Magnetic chamfers represent a significant advancement in precast concrete manufacturing technology, offering concrete producers a superior alternative to traditional chamfering methods. As detailed throughout this comprehensive guide, these innovative tools provide numerous advantages that directly impact production efficiency, product quality, and overall operational costs.
The key takeaways regarding magnetic chamfers include:
-
Efficiency Revolution: Magnetic chamfers dramatically reduce formwork preparation time, enabling faster production cycles and increased throughput for precast concrete operations.
-
Quality Enhancement: The precise positioning and secure attachment provided by magnetic systems ensure consistent, high-quality chamfered edges across all manufactured elements, reducing defects and enhancing product appearance.
-
Economic Advantage: Despite higher initial investment compared to traditional methods, magnetic chamfers deliver substantial long-term cost savings through extended service life, reduced labor requirements, and decreased material waste.
-
Versatility: Available in various sizes, angles, and configurations, magnetic chamfers can be adapted to virtually any precast concrete application from structural elements to decorative architectural features.
-
Sustainability Impact: The reusable nature of magnetic chamfers significantly reduces waste compared to disposable chamfer systems, aligning with modern sustainability goals in construction materials manufacturing.
For precast concrete manufacturers looking to optimize their production processes, we recommend:
-
Conduct a production workflow analysis to identify specific areas where magnetic chamfers could deliver the greatest immediate benefits.
-
Begin with a targeted implementation in high-volume production lines to maximize initial return on investment.
-
Invest in proper staff training to ensure optimal utilization of magnetic chamfer technology.
-
Establish a regular maintenance protocol to maximize the service life of magnetic chamfer components.
-
Partner with experienced suppliers like Horizon Magnetic who can provide technical support and customized solutions for specific applications.
As the precast concrete industry continues to evolve toward more efficient, precise, and sustainable production methods, magnetic chamfers have emerged as an essential tool for manufacturers committed to quality and operational excellence. By embracing this technology, precast concrete producers can gain a significant competitive advantage in today's demanding construction marketplace.
For more information about Horizon Magnetic's complete range of magnetic chamfer solutions for precast concrete applications, visit www.horizonmagnet.com or contact our technical support team for personalized assistance with your specific production requirements.